Der Schlüssel zum Erfolg durch Anwenden von Tailored Fiber Placement, kurz TFP
von Matteo Moretti, Projektmanager ZSK TECHNICAL EMBROIDERY SYSTEMS
Dieser Artikel soll als Leitfaden dienen, um die Vorteile der Verwendung der TFP-Technologie hervorzuheben und zu erläutern, wann und wie diese Technologie die Standardfertigung vollständig ersetzen sollte oder wie die Technologie in bestehende Prozesse integriert werden könnte.
In den letzten Jahren war das Wachstum von Technical Embroidery Systems exponentiell. Von ZSK STICKMASCHINEN entwickelte technische Stickmaschinen sind mittlerweile gut etabliert und werden hauptsächlich in der Automobil-, Luft- und Raumfahrt-, Sport- und Freizeitindustrie eingesetzt. Unter den zahlreichen technischen Sticktechnologien (d. H. Tailored Wire Placement, intelligente Textilien, E-Textilien, funktionelle Pailletten) erfährt das Tailored Fiber Placement (TFP) besonders das größte Interesse und die größte Nachfrage in der Industrie für Verbundwerkstoffe.
TFP-Stickmaschinen arrangieren und nähen einen Faserkabel auf einem kompatiblen Trägermaterial genau dort, wo die Verstärkung für die strukturelle Leistung am dringendsten benötigt wird. Mit TFP-Stickmaschinen kann der Benutzer nahezu netzförmige Vorformlinge erstellen, die eine einzigartige Rolle im Herstellungsprozess spielen. Durch die Implementierung von Vorformlingen in Netzform werden Verbundteile zunehmend kostengünstiger, während Abfallmaterial reduziert und die Struktur stark optimiert wird.
Wie und wann sollte man diese Technologie für Teile zur Herstellung von Verbundwerkstoffen implementieren? Welche Materialien sollten verwendet werden? Dieses Wissen ist für die meisten technischen Kunden von ZSK STICKMASCHINEN der Schlüssel zum Erfolg und zur Innovation.
TFP unter Verwendung von thermoplastischen Mischfasergarnen.
Mischgarne bestehen aus einer Mischung aus Thermoplast und Verstärkungsfaser. Während die neuesten Verstärkungsfasern normalerweise Kohlenstoff oder Glasfaser sind, könnte die thermoplastische Faser Nylon (PA6), Polypropylen (PP), thermoplastisches Polyurethan (TPU) oder Polyetheretherketon (PEEK) sein. Die Art des zu verwendenden Thermoplasten wird hauptsächlich in Abhängigkeit von den strukturellen Anforderungen der Endproduktanwendung gewählt. Aus dem gleichen Grund konnte der gewünschte Anteil von Faser zu Volumen während des Vermischungsprozesses variiert werden, wodurch die Gleichmäßigkeit des Verbundmaterials von Charge zu Charge erhöht wurde.
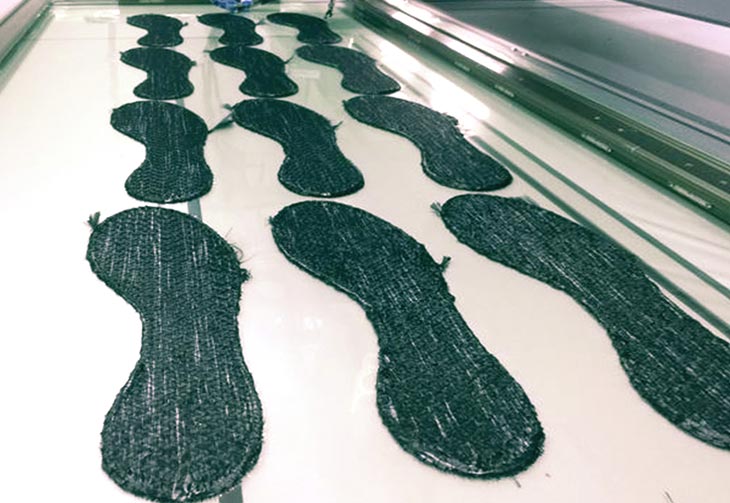
Abb.1: Eine Charge gemischter thermoplastischer Preforms.
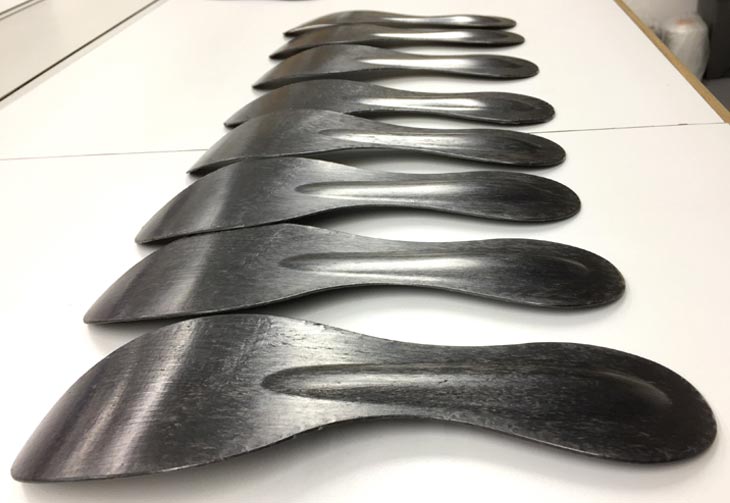
Abb. 2: Die Preforms nach dem Formen in der Presse von weniger als 3 Minuten.
Bei Preforms, die aus Mischgarnen hergestellt wurden, muss beim Formen kein zusätzliches Harz eingespritzt werden. Die thermoplastische Faser, die normalerweise zum thermoplastischen Trägermaterial passt, schmilzt und wirkt als Bindungsmatrix in der Verbundstruktur.
Dies führt zu einer drastischen Beschleunigung und Automatisierung des gesamten Herstellungsprozesses von Verbundwerkstoffen. Entsprechend entworfene und formoptimierte TFP-Preforms werden einfach in die Formen eingebracht und daher im Rahmen des Formpresszyklus für thermoplastische Materialien durch Erhitzen und Abkühlen zu den fertigen Teilen verfestigt.
Die Einfachheit der Nachbearbeitung wird streng von der Geometrie des Teils und dem Design der Form bestimmt. Bei komplexeren Teilen müssten die Kanten möglicherweise CNC-beschnitten werden. Stattdessen würden flachere Komponenten (wie die in Abb. 1 und 2 gezeigte innere Schuhsohle aus Verbundwerkstoff) in geschlossenen Formen netzförmig verfestigt, wobei die Kanten manuell und schnell entgratet würden.
Die Sport- und Freizeitindustrie zeigt begeistertes Interesse an der Implementierung der TFP-Technologie unter Verwendung von thermoplastischen Mischgarnen, die es Unternehmen ermöglicht, innovative, leichtere und leistungsfähigere Produkte zu einem wettbewerbsfähigen Preis auf den Markt zu bringen. Schließlich sind die resultierenden Produkte tendenziell nachhaltiger, da sie am Ende ihres Lebenszyklus wieder in neue Formen geschmolzen werden können.
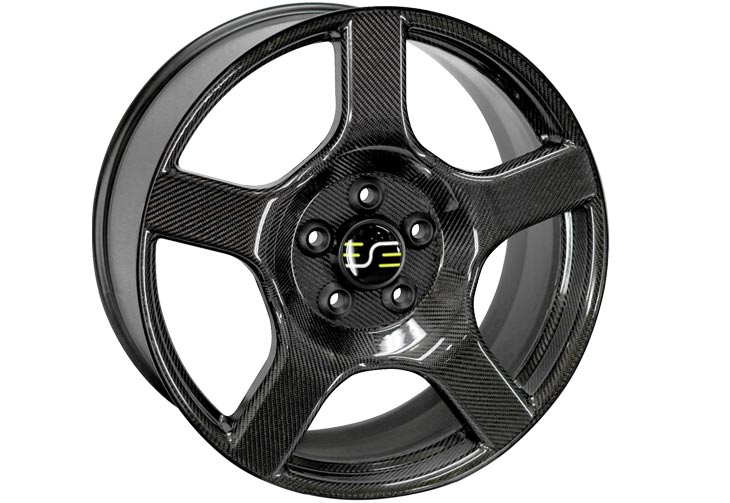
Abb. 3: Einteilige Carbonfaserfelge von ESE
TFP mit reinen Fasergarnen
Preforms, die aus reinen Fasergarnen (dh Carbonfaser, Glasfaser, Aramidglasfaser, Aramidfaser) hergestellt wurden, sollten als Verstärkung für das endgültige Verbundprodukt betrachtet werden, um in den bestehenden Herstellungsprozess wie Resin Transfer Moulding (RTM) oder Resin Infusion Moulding (RIM) integriert zu werden.
Ein gutes Beispiel ist das von ESE Carbon in den USA entwickelte Five Spokes Carbon Fiber Wheel (Abb. 3).
Carlos Hermida, CEO von ESE Carbon, erklärte in einem seiner jüngsten Interviews: „Die Technologie hat es dem Unternehmen ermöglicht, den Schichtverbrauch um bis zu 50% zu senken, wodurch ein vereinfachter Auflegeprozess geschaffen und Abfall minimiert wurde. Der Kohlefaserabfall wurde durch die Verwendung von TFP von etwa 40% bei herkömmlichen Kohlefasergeweben auf weniger als 10% reduziert. Darüber hinaus hat die Technologie zu einer verbesserten Auflegequalität, einer optimierten Faserorientierung und einer erhöhten Designflexibilität geführt. “
Abbildung 3 zeigt jeweils den „Radverstärkungsvorformling“, der mit der technischen Maschine TFP von ZSK TECHNICAL EMBRODERY SYSTEMS erstellt wurde, und das endgültig geformte E2-Carbonrad mit fünf Speichen. Der gleiche Anwendungs- und Anwendungsfall der Technologie wird von vielen großen ZSK-Kunden in der Automobil- und Luftfahrtindustrie weitgehend übernommen.
Wenn jedoch die niedrigere Produktivitätsrate das Hauptanliegen bei der Verwendung der TFP-Technologie war, hat ZSK Technical Embroidery Systems seine technischen Maschinen jetzt durch eine Reihe patentierter Innovationen auf die nächste Stufe gebracht, die die Ablagerung von Fasern beschleunigen und die Technologie noch weiter verbessern und die sogar für größere Preforms geeignet sind.
Vor weniger als einem Jahr hat ZSK STICKMASCHINEN die HV-TFP-Technologie eingeführt.
Das Prinzip ist ziemlich einfach: Zwei Rovings werden gleichzeitig abgelegt, wobei jedes mit einer linearen Dichte mehr als zweimal schneller als im eigentlichen Prozess genäht wird. Diese neue Funktionalität in Kombination mit der schnellen Faserverlegung ermöglicht es dem Hersteller, die Produktivität der Maschine zu steigern und so den Nutzen und die anwendbare Verwendung von TFP auch für große Bauteile zu erhöhen.
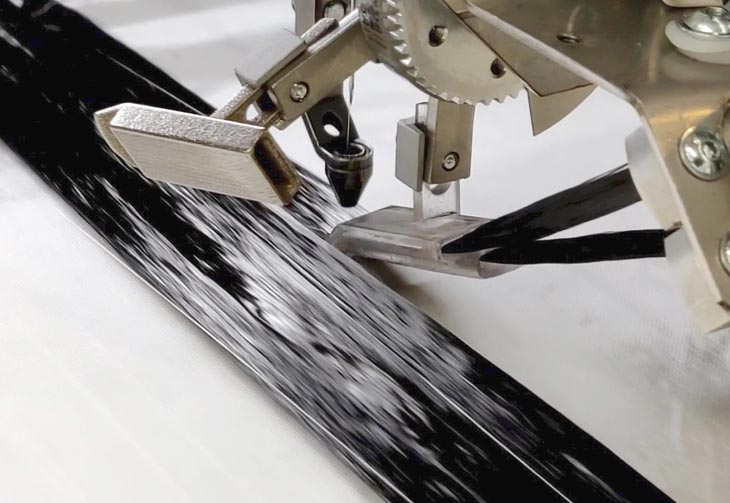
Abb. 4: Schnelle Faserverlegung + HV-TFP auf ZSK Technical Embroidery Systems
Zusammenfassend lässt sich sagen, dass TFP je nach Produktabmessungen, Materialien und strukturellen Anforderungen eine wertvolle Ressource für die Konstruktions- und Fertigungsgemeinschaft von Verbundwerkstoffen darstellt. Wenn Sie duroplastische Verbundteile in Betracht ziehen, sollte TFP im Vergleich zu den bestehenden Herstellungsverfahren als „Plus“ angesehen werden und für die Herstellung kleiner bis großer Bewehrungsteile geeignet sein.
Andererseits könnte TFP bei Verbundteilen auf Thermoplastbasis als Ersatz für Standardfertigungsverfahren für die Herstellung kleiner bis mittlerer Verbundprodukte angesehen werden. In beiden Fällen sind die offensichtlichen Vorteile der TFP-Technologie, die durch die technischen Innovationen von ZSK STICKMASCHINEN unterstützt wird, der Grund für das beträchtliche und konstante Wachstum in den letzten Jahren, obwohl die Produktion in unterschiedlichen Maßstäben und in verschiedenen Branchen abgeschlossen ist.