FreePreg - eine gesamtheitliche Prozesskette für den intelligenten Einsatz von Tailored Fiber Placement
von Max Schwab und Andreas Bündgens vom Institut für Textiltechnik (ITA) der RWTH Aachen University
Bauteile aus Faserverbundkunststoffen (FVK) überzeugen durch sehr geringes Bauteilgewicht bei gleichzeitig überragenden mechanischen Eigenschaften, wie z. B. Steifigkeit und Festigkeit. Die Reduktion von Strukturgewicht stellt noch immer eine zentrale Aufgabe für die Transportmittel Automobil oder Flugzeug dar. Das Tailored Fibre Placement (TFP) kann dabei eine Schlüsseltechnologie sein, ausgewählte hochbelastete Bauteile hinsichtlich des Gewichts weiter zu optimieren.
Derzeit gibt es jedoch noch immer Hürden, wieso dieses Verfahren nur in Nischen eingesetzt wird. Im Projekt „FreePreg“ hat sich das Institut für Textiltechnik (ITA) der RWTH Aachen University das Ziel gesetzt, eine gesamtheitliche Prozesskette für das TFP-Verfahren zu entwickeln und damit ein größeres Anwendungsspektrum zu generieren.
1. Wieso sind vorimprägnierte Textilien für hochbelastete Bauteile wichtig?
Das TFP-Verfahren stellt ein direktes Verfahren für die Textilherstellung für FVK-Bauteile dar (sog. Direktes Preforming). Diese Textilstrukturen (sog. Preforms) müssen anschließend noch mit einem Matrixwerkstoff, z. B. Epoxidharze imprägniert werden. Bei der Imprägnierung findet unter Temperatur, Zeit und ggf. Druck das Aushärten (sog. Konsolidierung) statt. Erst danach kann das Bauteil eingesetzt werden. Aufgrund der Vielzahl der notwendigen Prozessschritte als auch der ständigen Überwachung des Prozesses für gleichbleibende Bauteilqualität, hat sich mehrheitlich die Verwendung von vorimprägnierten Textilhalbzeugen (sog. Prepregs) durchgesetzt. Hierbei werden die Prepreg-Lagen in die entsprechende Werkzeugform drapiert und nachträglich wird das Material unter Temperatur, Zeit und ggf. Druck, z. B. in einem Autoklav ausgehärtet. Dabei wird ein Faservolumengehalt von bis zu 60 % erreicht.
Der Nachteil stellt bei diesen Verfahren die Limitierung verfügbarer Prepreg-Textilien dar. Dabei werden in großen Mengen Gewebe oder auch Gelege verarbeitet. Diese weisen jedoch eine vordefinierte Faserausrichtung im Halbzeug vor, z. B. 0° und 90° bei Geweben. Dadurch können die hochbelastbaren Verstärkungsfasern, wie z. B. Carbonfasern nicht mehr in Belastungsrichtung der Bauteile ausgerichtet werden. Dies führt zum einen zu deutlich höheren Mengen und Lagen von Prepreg um auch geforderte Sicherheitsfaktoren zu erreichen. Zum anderen entstehen dabei größere Mengen an Materialverschnitt, wenn es sich insbesondere um komplexe Bauteil-Geometrien handelt.
Die Verschnittraten können bei Geweben zwischen 30 % und 50 % liegen. Um die Verschnittraten zu reduzieren, bietet sich die TFP-Technologie an. Aktuell gibt es jedoch keine Möglichkeit, TFP-Preforms mit klassischen Prepreg-Halbzeugen für duroplastische FVK-Bauteile zu kombinieren.
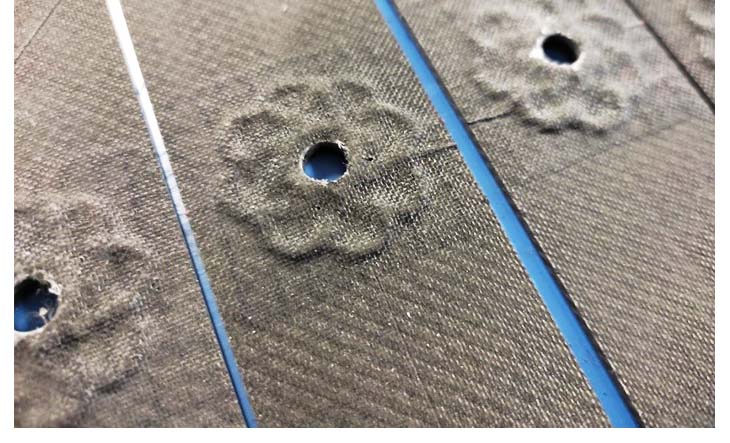
2. Wie kann die Herstellung von TFP-Bauteilen noch nachhaltiger gestaltet werden?
TFP-Halbzeuge zeichnen sich dadurch aus, dass die Verstärkungsfasern dabei in Kraftrichtung im Bauteil ausgerichtet werden können. Das ermöglicht beim Erstellen der Stickmuster auch, dass die Fasern möglichst nah an der Endkontur der Bauteile liegen. Damit kann der Faserverschnitt in einem Bauteil bis unter 5 % reduziert werden. Das TFP-Verfahren ist somit ein Textilverfahren, mit dem sehr materialeffizient produziert werden kann. Allerdings sind beim TFP-Fertigungsverfahren gegenüber anderer Textilverfahren weitere Hilfsstoffe notwendig, wie z. B. Stickfaden oder Trägermaterial.
Als Trägermaterial kann beispielsweise ein Carbonfaser-Vliesstoff eingesetzt werden, sodass sich keine Fremdstoffe im späteren Bauteil befinden. Vielmehr gibt es mittlerweile die Möglichkeit, dass diese Vliesstoffe aus recycelten Carbonfaserfilamenten produziert werden. Durch den Einsatz von Carbonfaser-Vliesstoffen können zusätzlich die anfallenden Carbonfaser-Materialabfälle im TFP-Prozess wieder in die Vliesstoff-Herstellung rückgeführt werden.
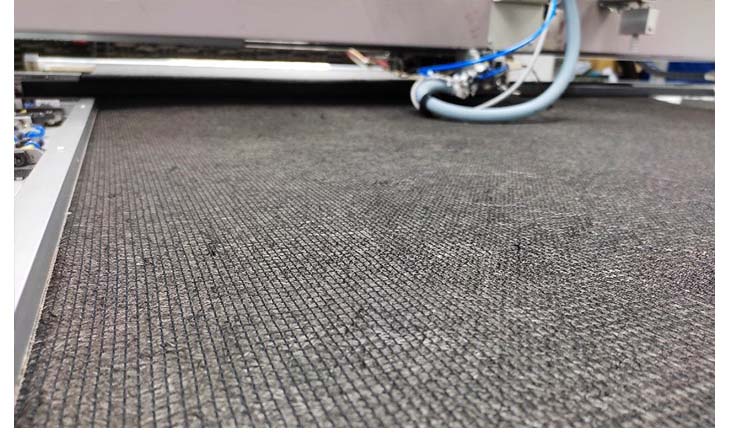
Bei der Prepreg-Beschichtung wird das Material großflächig mit einer Harzschicht imprägniert. Für die Imprägnierung von TFP-Preforms kann der nachgelagerte Beschichtungsprozess allerdings so eingestellt werden, dass unbeschichtete Stellen im Vliesstoff auch wieder recycelt werden können.
Im Projektvorhaben „FreePreg“ haben sich Wissenschaftler des ITA aus Aachen daher genau dieses Trägermaterials bedient (vgl. Abb. 2).
Die Idee: Carbonfaser-Vliesstoff als Trägermaterial für den TFP-Stickprozess und den nachgelagerten Beschichtungsprozess. Eine kostengünstige Serienproduktion beider Verfahren kann Rolle-zu-Rolle durchlaufen werden, sodass auch eine von beschichteten TFP-Halbzeugen (sog. FreePregs) möglich ist. Alles unter den Gesichtsprunkten der Nachhaltigkeit.
3. Wie kann die Performance von Leichtbauteilen durch den Einsatz von TFP gesteigert werden?
Kann der Einsatz von Carbonfaser-Rezyklat die gleiche mechanische Performance vorweisen? Klare Antwort: ja! Wird das TFP-Verfahren bzw. die Verstärkungsstrukturen lokal aufgebracht, kann die Performance lokal drastisch gesteigert werden. Im Projekt FreePreg wurden dafür gebohrte Zugproben sowie Proben mit metallischen Krafteinleitungselementen (sog. Inserts) untersucht. Als Lochverstärkung wurden auf die Proben blumenartige Lochverstärkungen auf die Prepreg-Laminate aufgebracht (s. Abb. 3).
In allen Fällen konnte gezeigt werden, dass die Lochverstärkungen einen großen Einfluss auf die FVK-Bauteilfestigkeit haben. Dabei konnten die Kerbzugfestigkeit um bis zu 34 %, die Ausreißkraft an Insert-Proben um bis zu 102 % maximiert werden. Vielmehr konnte dabei auch gezeigt werden, dass das Aufbringen von vorimprägnierten TFP-Verstärkungen (nach dem FreePreg-Ansatz) die Festigkeit im Verbund weiter erhöht. Nicht vorimprägnierte Verstärkungen bzw. Vliesstoffe haben dagegen einen negativen Einfluss auf die Konsolidierung der FVK-Bauteile. Durch die verbesserten mechanischen Eigenschaften können bei geforderter Performance die leichteren FreePreg-Einleger benutzt werden.
4. Was sind mögliche Anwendungsfelder und wie sieht ein Serienfertigungsprozess aus?
Das Demonstrator-Bauteil für die Validierung der entwickelten Prozesskette stellt ein Deckenpanel für den Flugzeuginnenraum dar. Dieses Bauteil weist einen klassischen Sandwich-Aufbau auf, bei den Prepreg-Decklagen ober- und unterhalb eines Wabenkerns angebracht sind. Im Bauteil sind dabei auf der Bauteil-Rückseite zwei Aussparungen zum Anbringen von Befestigungselementen. Diese Befestigungselemente sollen die Montage des Deckenpanels in der Deckenstruktur im Flugzeuginnenraum ermöglichen. Im Projektvorhaben „FreePreg“ wurden diese Aussparungen sowie zwei weitere Stellen zur Implementierung von TFP-Lochverstärkungen ausgewählt. Insgesamt wurden somit vier Lochverstärkungen für Krafteinleitungselemente auf der Bauteil-Rückseite hergestellt (vgl. Abb. 4).
Zur Vereinfachung wurde im Projekt die Annahme getroffen, dass aufgrund der hervorragenden mechanischen Eigenschaften der TFP-Lochverstärkungen im Referenzbauteil je zwei Decklagen notwendig sind, um die gleiche mechanische Performance an den Lochverstärkungen zu erzielen.
Aufgrund der überragenden mechanischen Eigenschaften der Lochverstärkungen kann somit lokal Material im Bauteil eingespart werden. Dabei kann eine der beiden Decklagen, die sich normalerweise oberhalb und unterhalb des Wabenkerns befinden, ersetzt werden.
Auf der Bauteil-Rückseite wird dann der FreePreg-Einleger eingelegt. Dieser besteht aus vier TFP-Lochverstärkungen, die auf einem Carbonfaser-Vliesstoff aufgestickt sind. Werden ganze Decklagen substituiert, ergibt sich zunächst eine Gewichtsreduktion von 23 %. Außerdem kann dadurch auch Ausgangsmaterial (Prepreg) sowie Prozesszeit für die Drapierung im Bauteil eingespart werden. Konkret: Reduktion der Materialkosten um 43 % und Reduktion der Prozesszeit um 18 %.
Für den genannten Anwendungsfall kann damit das Strukturgewicht im Flugzeuginnenraum reduziert werden. Aber die TFP-Lokalverstärkungen sind universal einsetzbar.
So können auch Lastgurte, Verstrebungen oder Lochverstärkungen in anderen FVK-Bauteilen integriert werden. Denkbar ist hier insbesondere eine Implementierung in Batteriekästen für die Elektromobilität der Zukunft. Aufgrund des hohen Gewichts der Batteriezellen ist hier struktureller Leichtbau enorm wichtig für die Reichweite und Performance der Autos. Das FreePreg-Verfahren kann insbesondere dort eingesetzt werden, wo hohe punktuelle oder linienartige Kräfte aufgenommen werden müssen.
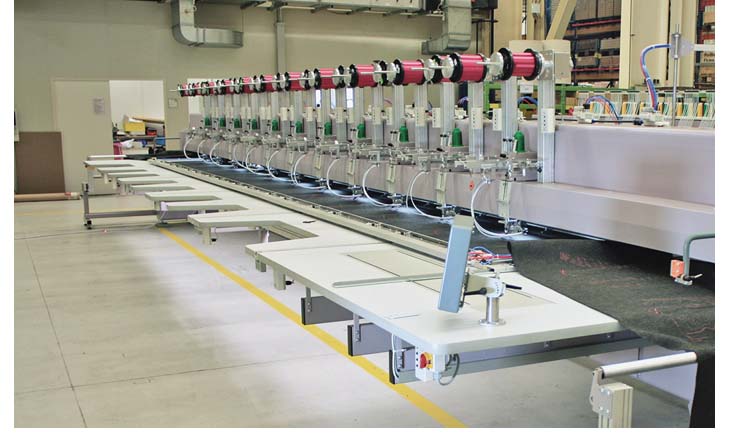
Eine Serienproduktion der FreePreg-Einleger für den gezeigten Demonstrator kann beispielsweise auf einer Mehrkopf-Stickmaschine vom Typ ZSK CZBW 1100-750-1200 realisiert werden (vgl. Abb. 5).
Die Stickmaschine hat 11 Stickköpfe und ein Stickfeld von 750 x 1200 mm². Somit können insgesamt 33 Preforms für das FreePreg-Bauteil (300 x 600 mm²) pro Stickfeld produziert werden.
Zusätzlich kann die Stickmaschine mit einer teil- und vollautomatisierten Rolle-zu-Rolle Vorrichtung ausgerüstet werden, die das Aufwickeln der TFP-Preforms ermöglicht.
Im Rahmen des FreePreg-Projekts wurde dafür der Produktionsprozess analysiert und eine Kostenkalkulation für die FreePreg-Herstellung durchgeführt. Bei einer jährlichen Ausbringungsmenge von ca. 85.000 Preforms können Stückkosten von unter 8.- € erreicht werden. Dabei sind Gemeinkosten- und Gewinnzuschlag bereits berücksichtigt.
Die Transferbeschichtung findet auf einer Beschichtungsanlage statt, die aufgrund der hohen Produktivität nur für eine Woche im 2-Schichtbetrieb läuft. Dabei können die 85.000 Preforms mit Harzmatrixwerkstoff beschichtet werden. Aufgrund der kalkulatorischen Kosten kann hier ein Prepreg-Preis von unter 14.- € (netto) inklusive Gemeinkosten- und Gewinnzuschlag erreicht werden.
Somit kann abschließend festgehalten werden, dass die FreePreg-Prozesskette eine Möglichkeit darstellt, nachhaltige, kosteneffiziente und gleichzeitig gewichtsoptimierte Strukturbauteile herzustellen. Dies wird durch den intelligenten und seriennahen Einsatz der TFP-Technologie ermöglicht.
5. Beteiligung im Projekt FreePreg
Die umfangreichen Entwicklungen im Projekt fanden zusammen mit dem projektbegleitenden Ausschuss statt (s. Infobox).
Neben beratenden Dienstleistungen konnten auch Untersuchungen auf Versuchsanlagen durchgeführt werden, die von den Partnern zur Verfügung gestellt wurden. So konnten die Rolle-zu-Rolle Versuche bspw. bei ZSK STICKMASCHINEN GmbH in Krefeld durchgeführt werden.
Der Demonstrator wurde mithilfe von Digel Sticktech GmbH & Co. KG, Pfullingen, und TFP Technology GmbH, Falkenstein, bei Diehl Aviation in Laupheim gefertigt.
Ohne die aktive Teilnahme des projektbegleitenden Projektausschusses wären die Entwicklung der Prozesskette sowie die Umsetzung des Demonstrator-Bauteils nicht möglich gewesen.
Wir danken den teilnehmenden Firmen für die aktive Zusammenarbeit sowie danken dem Bundesministerium für Wirtschaft und Klimaschutz (BMWi) für die Förderung des Forschungsprojektes „FreePreg“ im Rahmen der Industriellen Gemeinschaftsforschung (IGF) des AiF Forschungsnetzwerks Mittelstand