FreePreg - a fully integrated process chain for the intelligent use of tailored fibre placement
by Max Schwab and Andreas Bündgens from the Institut für Textiltechnik (ITA) der RWTH Aachen University
Components made of fibre-reinforced plastics (FRP) are convincing due to their very low component weight and simultaneously outstanding mechanical properties, such as stiffness and strength. The reduction of structural weight still represents a central task for the means of transport automobile or aircraft. Tailored Fibre Placement (TFP) can be a key technology for making selected highly stressed components even more weight-optimised.
At present, however, there are still hurdles, which is why this process is only used in certain niches. In the "FreePreg" project, the Institute of Textile Technology (ITA) of RWTH Aachen University has aimed to develop a holistic process chain for the TFP process and thus generate a wider range of applications.
1. Why are pre-impregnated textiles important for highly stressed components?
The TFP process is a direct process for the production of textiles for FRP components (so-called direct preforming). These textile structures (so-called preforms) must then be impregnated with a matrix material, e.g. epoxy resins. During impregnation, curing (so-called consolidation) is performed under temperature, time and, if necessary, pressure. Only then can the component be used. Due to the large number of necessary process steps and the constant monitoring of the process for consistent component quality, the use of pre-impregnated textile semi-finished products (so-called prepregs) has become widely accepted. Here, the prepreg layers are draped into the corresponding mould and the material is subsequently cured under temperature, time and, if necessary, pressure, e.g. in an autoclave. A fibre volume content of up to 60% is achieved.
The disadvantage of these processes is the limited availability of prepreg textiles. Woven fabrics or scrims are processed in large quantities. However, these have a predefined fibre orientation in the semi-finished product, e.g. 0° and 90° for woven fabrics. This means that the highly resilient reinforcing fibres, such as carbon fibres, can no longer be aligned in the load direction of the components. On the one hand, this leads to significantly higher quantities and layers of prepreg in order to achieve the required safety factors. On the other hand, this results in larger amounts of material waste, especially when it comes to complex component geometries.
The waste rates can be between 30 % and 50 % for woven fabrics. In order to reduce the waste rates, the TFP technology offers itself. However, there is currently no possibility to combine TFP preforms with classic prepreg semi-finished products for thermoset FRP components.
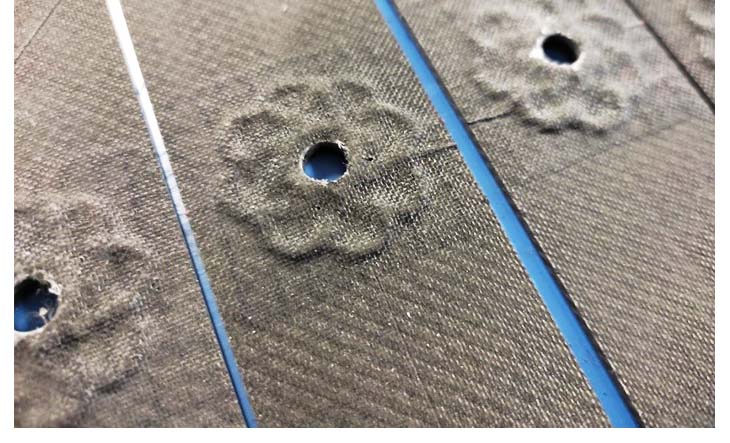
2. How can the production of TFP components be made even more sustainable?
TFP semi-finished products are characterised by the fact that the reinforcing fibres can be aligned in the direction of force in the component. This also allows the fibres to be as close as possible to the final contour of the components when creating the embroidery patterns. In this way, the fibre waste in a component can be reduced to less than 5 %. The TFP process is thus a textile process with which production can be very material-efficient. However, compared to other textile processes, the TFP production process requires additional auxiliary materials, such as embroidery thread or carrier material.
A carbon fibre nonwoven, for example, can be used as a substrate so that there are no impurities (e.g. other material) in the later component. In fact, it is now possible for these nonwovens to be produced from recycled carbon fibre filaments. By using carbon fibre nonwovens, the carbon fibre material waste produced in the TFP process can also be recycled back into the nonwoven production process.
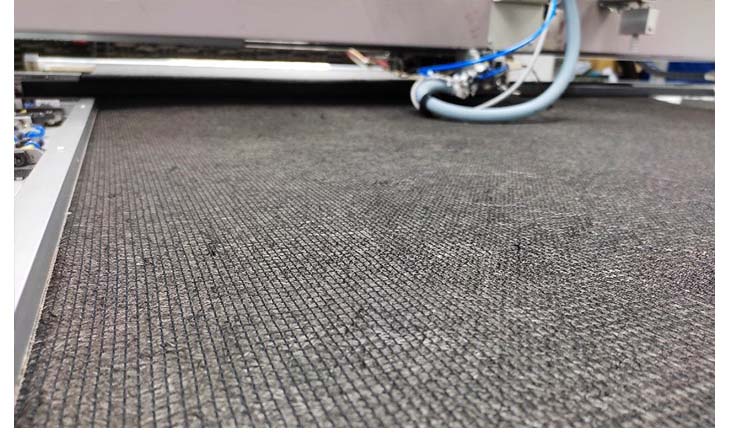
In the prepreg coating process, the material is impregnated with a resin layer over a large area. For the impregnation of TFP preforms, however, the downstream coating process can be adjusted so that uncoated areas in the nonwoven can also be recycled again.
In the "FreePreg" project, scientists from ITA in Aachen have therefore used precisely this carrier material (cf. Figure 2).
The idea: carbon fibre nonwoven as a carrier material for the TFP embroidery process and the downstream coating process. A cost-effective series production of both processes can be run roll-to-roll, so that a production of coated TFP semi-finished products (so-called FreePregs) is also possible. All under the aspect of sustainability.
3. How can the performance of lightweight components be improved by using TFP?
The answer is clearly yes! If the TFP process or the reinforcement structures are applied locally, the performance can be drastically increased locally. In the FreePreg project, drilled specimens for notch tensile testing as well as specimens with metallic inserts were examined for this purpose. Flower-like hole reinforcements were applied to the prepreg laminates as hole reinforcement (see Figure 3).
In all cases, it could be shown that the hole reinforcements have a significant impact on the FRP component strength. The notch tensile strength could be maximised by up to 34 %, the pull-out force on insert samples by up to 102 %. It was also shown that the application of pre-impregnated TFP reinforcements (according to the FreePreg approach) further increases the strength in the composite. Non-preimpregnated reinforcements or nonwovens, on the other hand, have a negative influence on the consolidation of the FRP components. Due to the improved mechanical properties, the lighter FreePreg inserts can be used if the required performance is achieved.
4. What are possible fields of application and what does a series production process look like?
The demonstrator component for the validation of the developed process chain is a ceiling panel for the aircraft interior. This component has a traditional sandwich structure in which prepreg cover layers are attached above and below a honeycomb core. There are two recesses in the back of the component for attaching fastening elements. These fastening elements are intended to enable the ceiling panel to be mounted in the ceiling structure in the aircraft interior. In the "FreePreg" project, these recesses and two other locations were selected for the implementation of TFP hole reinforcements. A total of four hole reinforcements for force introduction elements were thus produced on the rear side of the component (cf. Fig. 4).
For simplification, the project assumed that due to the excellent mechanical properties of the TFP hole reinforcements, two cover layers are necessary in each case in order to achieve the same mechanical performance at the hole reinforcements.
Due to the superior mechanical properties of the hole reinforcements, material can thus be saved locally in the component. One of the two cover layers, which are normally located above and below the honeycomb core, can be replaced.
The FreePreg inlay is then placed on the component rear side. This consists of four TFP hole reinforcements embroidered onto a carbon fibre non-woven fabric. If entire cover layers are substituted, this initially results in a weight reduction of 23 %. In addition, this can also save raw material (prepreg) as well as process time for draping in the component. Specifically: reduction of material costs by 43 % and reduction of process time by 18 %.
For the application mentioned, the structural weight in the aircraft interior can thus be reduced. But the TFP local reinforcements can be used universally.
Thus, load belts, struts or hole reinforcements can also be integrated in other FRP components. Implementation in battery cases for the electro mobility of the future is particularly conceivable here. Due to the high weight of the battery cases, structural lightweight construction is enormously important here for the range and performance of the cars. The FreePreg process can be used in particular where high punctual or linear forces have to be absorbed.
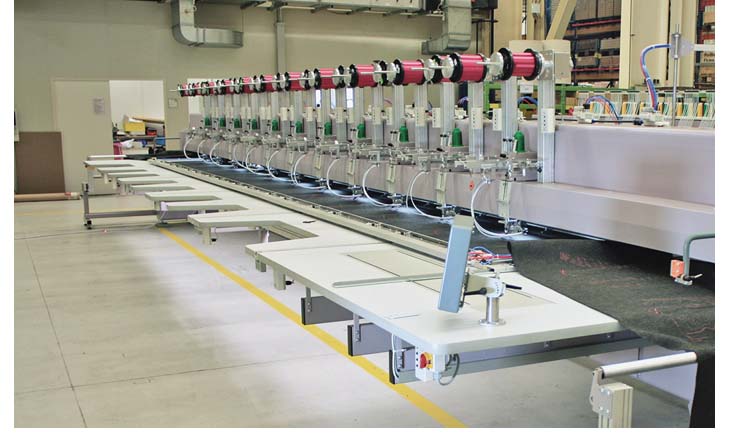
Series production of the FreePreg inserts for the demonstrator shown can be realised, for example, on a multi-head embroidery machine of the type ZSK CZBW 1100-750-1200 (cf. Figure 5).
The embroidery machine has 11 embroidery heads and an embroidery field of 750 x 1200 mm². Thus, a total of 33 preforms for the FreePreg component (300 x 600 mm²) can be produced per embroidery field.
In addition, the embroidery machine can be equipped with a partially and fully automated roll-to-roll device that enables the winding of the TFP preforms.
Within the FreePreg project, the production process was analysed for this purpose and a cost calculation for FreePreg production was carried out. With an annual output of about 85,000 preforms, unit costs of less than €8 can be achieved. Overhead and profit surcharges are already taken into account.
The impregnation process takes place on a coating line that runs in 2-shift operation for only one week due to the high productivity. In this process, the 85,000 preforms can be coated with resin matrix material. Due to the calculatory costs, a prepreg price of less than € 14 (net) including overhead and profit surcharge can be achieved here.
Thus, it can be concluded that the FreePreg process chain represents a possibility to produce sustainable, cost-efficient and at the same time weight-optimised structural components. This is made possible by the intelligent and close-to-production use of TFP technology.
5. Project partners participating in FreePreg
The large-scale developments in the project took place together with the project-accompanying committee (see infobox).
In addition to advisory inputs, tests could also be carried out on test equipment provided by the partners. For example, the roll-to-roll tests could be carried out at ZSK Stickmaschinen GmbH in Krefeld.
The demonstrator was built with the help of Digel Sticktech GmbH & Co. KG, Pfullingen, and TFP Technology GmbH, Falkenstein, at Diehl Aviation in Laupheim.
Without the active participation of the project committee, the development of the process chain and the implementation of the demonstrator component would not have been possible.
We would like to thank the Federal Ministry for Economic Affairs and Climate Action (BMWK) for funding the research project within the framework of the Industrial Joint Research (IGF) of the AiF Research Network for Small and Medium-Sized Enterprises.