E-Textiles – Traditional Fabrics with Functions
E-textiles, or the ability to embed electronics and their electrical properties into fabrics, allow for a new class of self-aware materials. They offer you the opportunity to confer functions upon traditional fabrics. These materials can have internal sensing capabilities as well as the ability to adapt themselves to various changing environments. In this way, they open doors to data collection that was not previously economic or even possible.
Technical embroidery offers a host of methods to create new e-textiles and to push the entire field forward. Due to embroidery’s high maneuverability, quick adaptability to new designs, and established scalability, embroidered systems are increasingly being sought after. The aim: to create prototypes and solutions for this ever-growing e-textiles market.
Conductive Connections
Technical embroidery can allow traditional circuit boards to be mechanically mounted to fabrics, while automatically creating conductive textile connections them. Aspects of traditional circuit board design such as creating conductive traces can also be incorporated using technical embroidery.
Electrical components have an ever-decreasing size. This opens a greater scope of design, e.g. mounting components to embroidered sequins. Moreover, sensors can be integrated exactly where they are needed in an automated process.
Technical embroidery systems offer solutions to two of the biggest challenges facing the e-textile industry. On the one hand, they enable the realization of a reliable interface between the electronic components and the textile and, on the other hand, the automated mass production of smart and e-textiles.
Our video takes you into the world of smart textiles, and shows how ZSK Stickmaschinen GmbH faces the challenges in today's volatile world.
It is easy to see that due to its high precision and many options, embroidery technology is an excellent tool for integrating functionalities into textiles.
Thus, with only 3 different embroidery heads, a wide variety of geometries of textile sensors, actuators, electrodes, functional LED's or RFID sequins, and even entire printed circuit boards (PCB's) with conductive threads can be integrated automatically and reliably. This wide range of possibilities always poses new challenges, but at the same time offers room for innovation.
With our engineering office 3E Smart Solutions, ZSK Stickmaschinen GmbH offers its customers a unique combination of technology and know-how transfer for the realization of their products. 3E Smart Solutions has set itself the goal to accompany your vision from prototype development to industrial production, and to provide holistic consulting support.
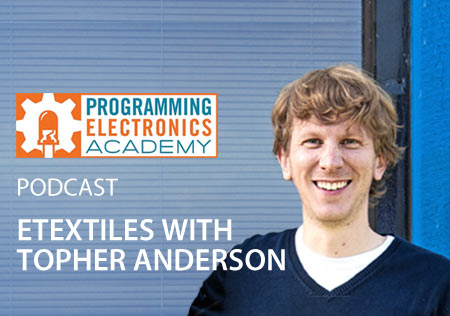
ETEXTILES WITH DR. TOPHER ANDERSON
A Podacst
Michael Chaich, owner of "Programming Electronics" in conversation with Dr. Topher Anderson, Technical Embroidery Manager, ZSK USA about e-textiles.
One of the most direct uses of technical embroidery is to quickly attach and stitch traditional printed circuit boards into fabric carriers. Stitching boards immediately into the structure of the textile reduces mechanical strains on the connectors while allowing the control and processing electronics to be physically closer to their supporting electronics. This can have a range of benefits such as increased signal to noise ratio, decreased mechanical fatigue based failure, and reduced need for additional connectors.
For electronics packaging, fabrics offer a new host of materials that not only house the electronics, but also provide functional advantages over traditional materials and processes.
Another advantage of technical embroidery in e-textiles manufacturing is the ability to embroider electrical connects automatically to the host board using various conductive threads. This process allows for the quick connection of potentially hundreds of electrical connections from a board to their fabric-hosted sensors. By registering the board during its embroidery to the host fabric, electrical connection points on the board are also registered for stitching. This can allow for a single stitched board to merge data from many sensor types into a single output.
By using techniques such as Tailored Wire Placement, highly conductive materials can be placed into the structure of the fabric. Thus, it is possible to create low resistance traces that better mimic traditional circuit board function. Size AWG 10 to AWG 40 wire has been successfully laid in this process.
Additionally, wire coatings such as enamel or PVC are unaffected by the embroidery process, opening a wide variety of insulative and coating materials. Furthermore, customized wires such as multicore and multifilament wires can be used to run multiple signals through a single conductive pass. Up to 32 signals in a single multicore line can be run, with the capability of going much higher.
Traditional sensors such as temperature sensors can be embroidered into a textile by embroidering their host circuit board into the textile or by including the sensor into a fiber carrier.
Embroidering additional sensor boards into the fabric is a straight forward method of quickly integrating capability and function. You can achieve a more elegant and compliant solution by embroidering sensors within a fiber carrier.
However, form fitting and haptic-sensitive textile based sensors are increasingly being investigated for their inclusion into a functional fabric. Thereby, properties of conductive fibers are helpful, e.g. in large surface areas. Thanks to variable resistivity and geometric conformability, solutions such as textile electrodes, stretch sensors, and sweat sensors can be reliably created.
Another method of functionalizing fabrics is the inclusion of embroidered LED sequins. By mounting the required electronics onto a traditional sequin carrier, LEDs can robotically be sewn into a garment during its creation. This has significant advantages over other e-textile processes as it does not require post-process soldering or additional conductive epoxies. In this way, the embroidery machine serves as a hybrid between traditional pick and place machines to select a component sequin off of a reel and a sequin machine as it stitches the component into the fabric’s structure.
Technical embroidery can be applied to radio frequency engineering through the use of new and geometrically tunable antennas. The shape of textiles in garments can vary dramatically from when the textile is being stored to when it is being worn. This means limitless possibilities generated by embroidering antennas of various tunable shapes. These designed textile antennas can have uniquely directional properties that traditional hard antennas do not have. As our world becomes increasingly wireless, textile antennas are an open and exciting area of research.
One of the more important thoughts to have when evaluating any e-textile prototype is its ability to quickly and cost effectively scale. As embroidery is a well-established textile process with many configurations for production machines, the risk to scaling is much lower compared to other less known e-textile processes.
In fact, many longstanding embroidery companies can even utilize their existing equipment setup to turn their machines from traditional embroidery to technical e-textiles embroidery.