How to make facemasks on embroidery machines
In this post, we will be documenting a few strategies to make facemasks with embroidery machines. These masks are not intended to replace N95 masks, but rather to supplement and protect the average user helping to free up other masks for medical professionals in the front lines on the battle with corona virus.
These masks are designed to be created on different types of embroidery machines in order to help automate and speed the process. Different designs are below detailed by different machine types and frame sizes.
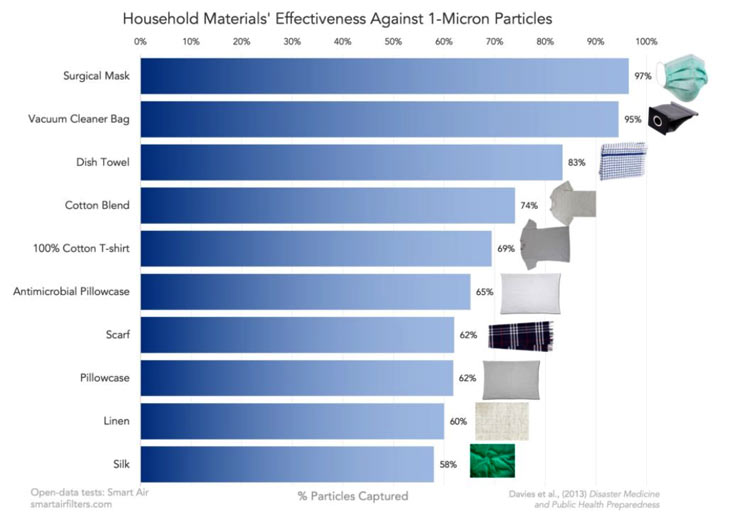
For fabric, many varieties and possibilities exist that have some level of effective filtration. In this study from 2013, some of the different types are evaluated. Some common fabrics can block a great majority of particles reducing the potential exposure risk. Many of the fabrics we have been exploring use felt and other nonwovens as the filtration media.
Additional designs that we have been exploring use readily available MERV12 or MERVE13 filters that are commonly used in household air filtration and available at hardware stores.
This material is a little more manual to extract from these finished filters, however frees up the N95 material for other medical uses. Therefore, these filters are perfect for smaller machines like the SPRINT series. This material is easily cut with the hot air cutter further increasing automation of a small operation.
In the first picture below we see the full air filter as it comes from the hardware store. This filter contains a large amount of MERV12 or MERV13 filtration media. This material does not subtract from existing medical supplies and fits great in SPRINT machines
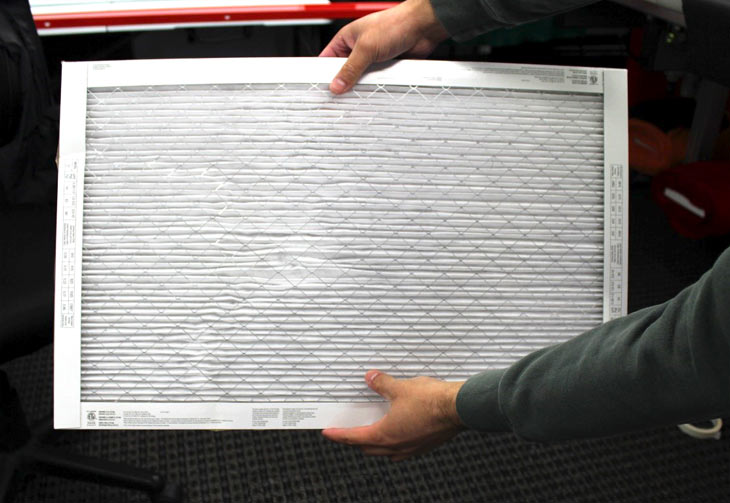
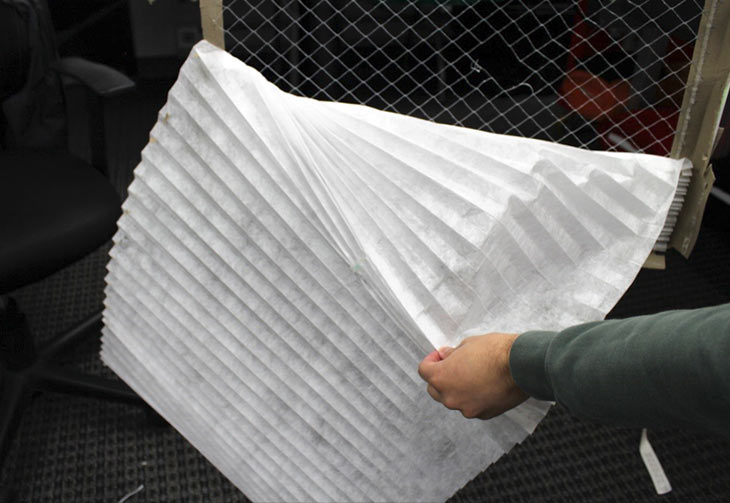
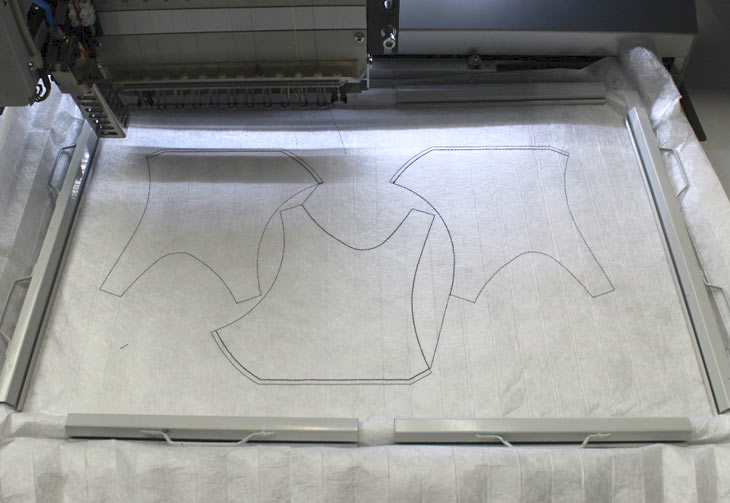
Multiple layer systems are currently being explored in which felt is embroidered as a carrier material to the MERV12 or MERVE 13 filtration media. This helps to support the design, create robustness, and further filters material. Multilayered systems can be an effective implementation.
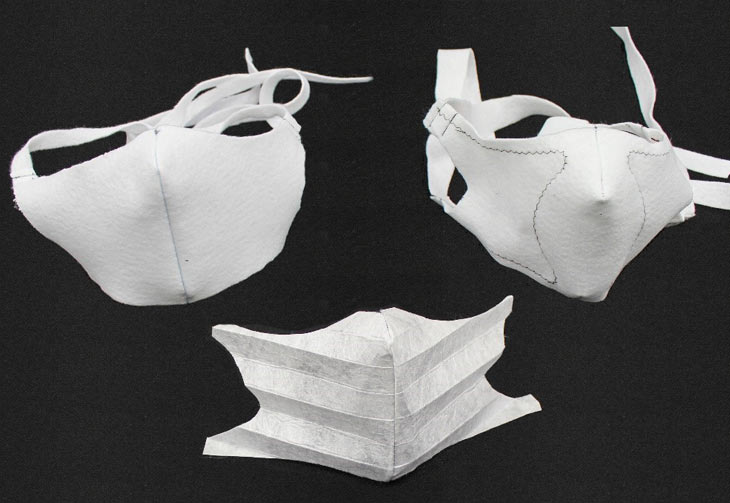
Masks made from the three methods presented.
In the image top left, a nonwoven masks that has been embroidered and cut with a HAC on a ZSK RACER. In the lower middle, a mask made from a MERV12 air filter on a ZSK SPRINT, and at the top right, a mask embroidered and cut on a JGVA with wire incorporated for a better seal against noses.
Design wise, masks should fit snuggly against the face with limited gaps between the mask and skin. One of the primary benefits of fabric masks is not just prevention of getting a disease, but rather prevention of spreading a disease you don’t know you have. Fabric masks help to contain the infected water droplets that spread the disease. For many diseases, there are carriers who feel limited or no effects of the disease however are infected, contagious, and can spread the disease. Minimizing the spread helps to flatten the curve reducing a critical overloading of the medical system.
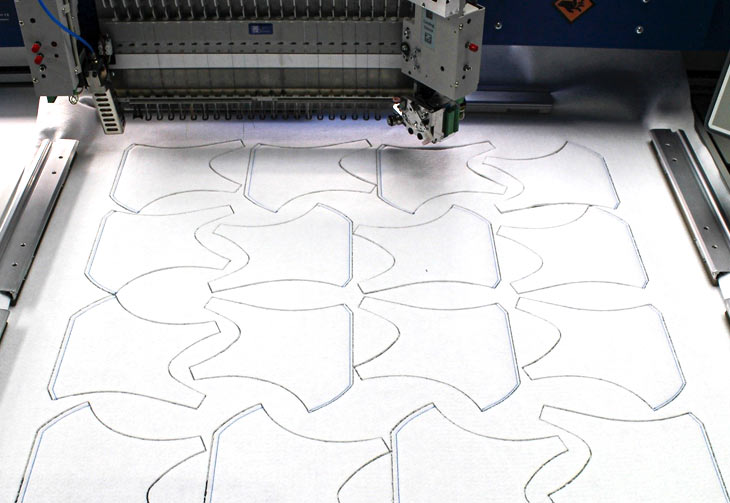
RACER 1XL with Hot Air Cutting
For the design of these masks, straps have not been included in the initial embroidery file to help save on material waste. Straps can be made of scraps of material (recommended for sustainability practices) or also made from elastic bands or cords. Some creativity is required here to maximize the process and efficiency. Straps function to hold the mask tightly against the face, and so many possibilities exist.
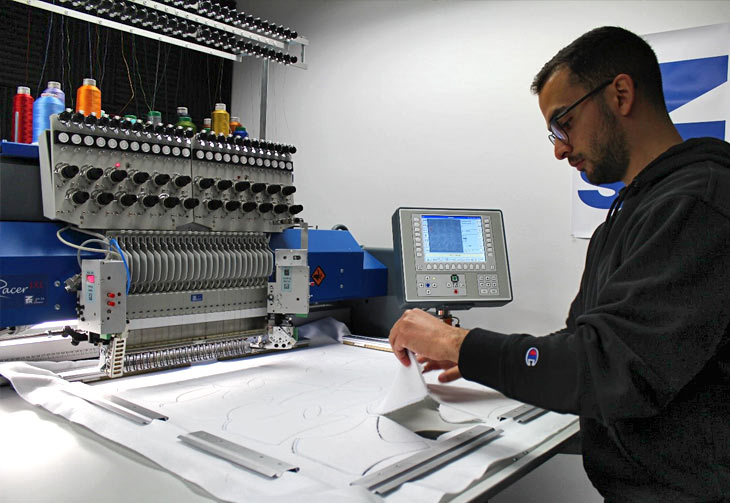
Using the Hot Air Cutting Device or short HAC allows for the pieces to be easily removed from the frame without additional need for cutting.
Some areas are experiencing an elastic shortage. Therefore, using scrap materials to create the ties can be a cost effective and environmentally conscience way of creating a tight hold to the face. In this example, pop rivets have been used to connect the straps.
In this example, the straps have been sewn to the mask.
For that we used a simple home sewing machine and used waste material for the straps that otherwise would have been disposed of.
Clean the Machines
Operationally, it is important to follow good laboratory practice. That means machines should be regularly cleaned with bleach, isopropyl alcohol (90%) or ethanol (90%) should be used to regularly disinfect hands and touch screens. Further possibilities of sterilization exist using ultraviolet type C light which has been show to sterilize various bacteria and viruses. If using UVC light, be very careful to ensure that no people are in the room when used as the light can cause sever skin burns, blindness, and other damage. Additionally, these lamps can produce ozone, so limited use and regular air venting is recommended. Please consult a professional for more questions before implementing such a solution.
Possibilities of Filters
Another possibility being explored is the production of small filter disks. These filter disks consist of an embroidered fabric disk in which activated charcoal can be filled. These disks resemble small teabags where the filter helps to both contain the carbon and filter out larger particles. The carbon then helps to further filter the microbes out of the air. These filters are closer in design to P100 filters, but require an additional filling step of activated charcoal.
Currently, we are standardizing the size of the disks so that different partners can 3D print or machine housing for them. As embroiderers, we can do what we do best: embroider filters. This way we can partner with other groups in our communities for them to create the housings that hold our filters. At the moment, a design standard has been made in the USA of a 4” diameter circular filter with ¼” thickness. By having a standard, we help to allow these filters to fit housings developed by partners thereby distributing the design and manufacturing effort so we can each focus on our specialties.
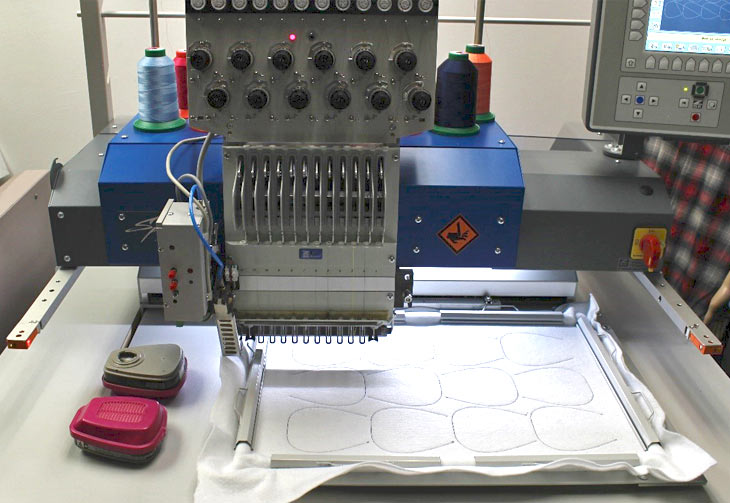
In this image, filters that fit into existing P100 filter cartridges are being embroidered with two layers of felt cut by the HAC. This allows for a tight pocket that can be filled with activated charcoal and quickly sealed on a sewing machine creating a filter.
Housings for these filters are being designed, prototyped, 3D printed, and manufactured by a variety of groups. These filters in cartridges/housings can be retrofitted onto existing scuba gear, water bottle face shields, and existing respirators using different connectors such as heat shrink tubing, 3D printed connector pieces, and other epoxy based polymers.
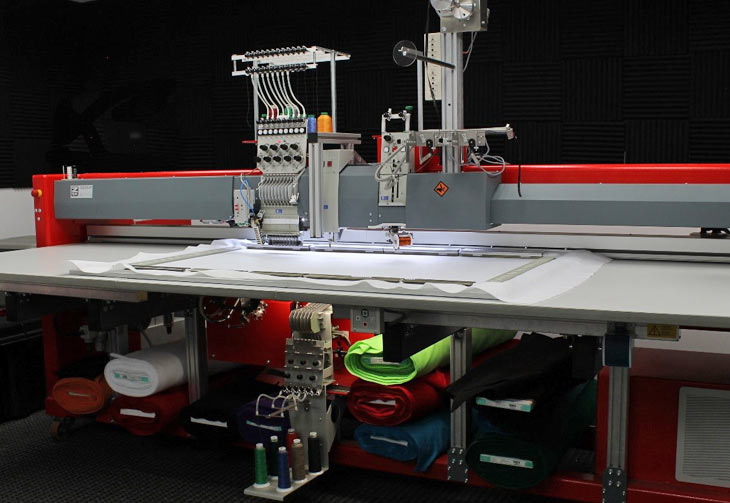
Shapes of Faces
For some face shapes, the existing facemask design does not allow for a tight seal against the bridge of the nose or the jawline.
Therefore, a JGVA machine was used to place 22 AWG copper wire down to give structure, stiffness, and bendability that can customize the shape similar to the bendable metal wire on N95 nosepieces.
After embroidery and wire placement, the fabric is ready to be cut. This fabric can be cut on a HAC or additionally by hand on the stitch line later.
Resulting wire reinforced facemask that bends and conforms tightly to the face.
Inside of the wire facemask.
Additional points that have not been addressed yet
- Making designs of masks that children want to wear and enjoy wearing
- Increasing the social desirability and ‘cool’ factor of masks so that people wear them constantly
- Materials suppliers that can create the nonwoven filter material in bulk
- Actual quality of the masks being produced, including access to better materials and processes
- Design improvements for comfort, wear ability, and visual aesthetic
Stay tuned
Further designs, improvements, and standards will be updated as we interact with different professionals in the field and receive feedback. Please check back for these new developments and improvements and feel free to use, redesign, and spread these ideas and files.
Additionally, please contact us if you have new developments, designs, or thoughts about how to proceed more efficiently.
Contact us via email: topher@zsk.de
Hopefully in this way we can help our communities be safer, healthy, and fight the spread of the corona virus.