Advantages & Unique Selling Points
ZSK has made tremendous progress in recent years to make TAILORED FIBRE PLACEMENT (TFP) attractive for many applications and mass production.
Overview:
Features | Technical Systems (Slide) | Whitepaper
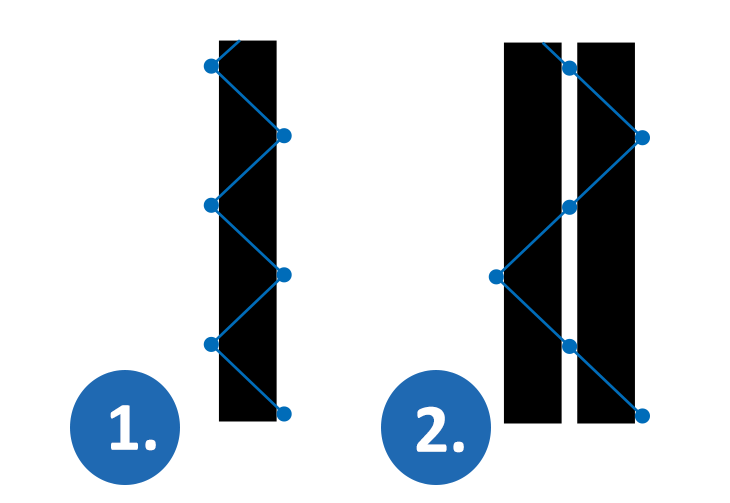
200%
increase in volume
High Volume - TFP (HV-TFP)
Together with our partner Nobrak SAS, ZSK has developed the parallel placement of 2 or more fibre strands.
This patented process doubles the placement volume of fibre strand, drastically increasing productivity for mass production.
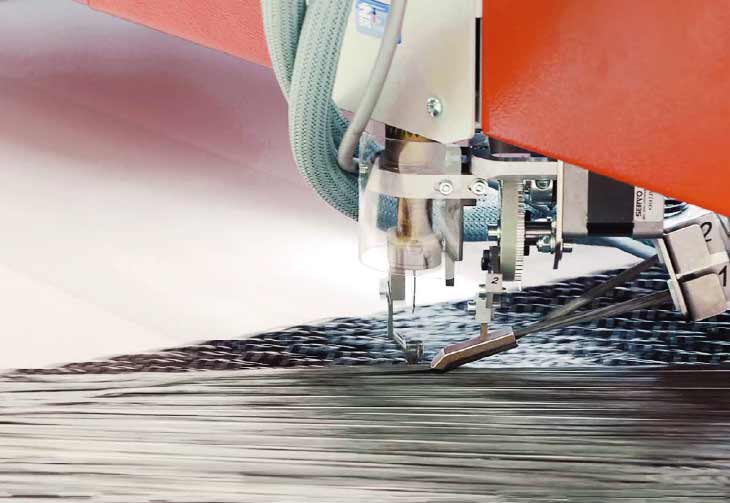
75%
Increase in output
Fast Fibre Laying
With this patented technology, the fibre strands are laid at high speed without stitches.
This method can be used in any angle but the fibre strands need to be laid in a straight line. Up to 8 layers can be laid in any angle, whereby the fibre strands of the last layer are fixed with continuous stitches, thus fixing the previous layers.
Fast fibre laydown brings up to 75% increase in output.
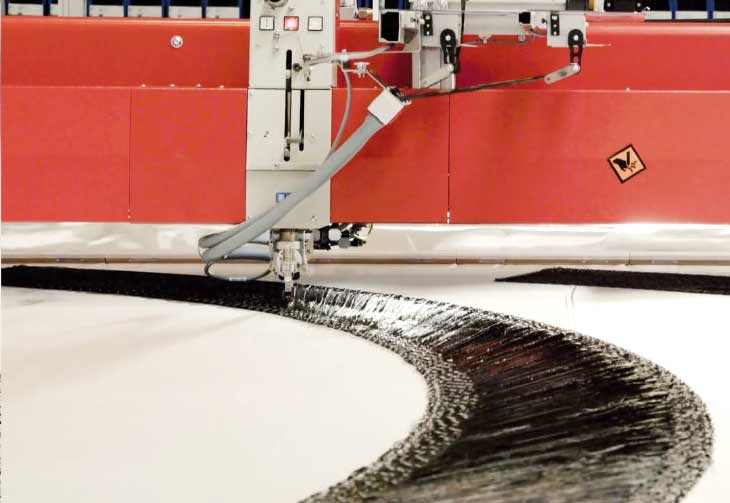
300%
Increase in performance
Combination of HV-TFP and Fast Fibre Laying
The combination of HV-TFP and Fast Fibre Laying achieves performance increases of up to 300% compared to the conventional TFP technology.
Feeding fibre strands
- Up to 4 fibre strands per head can be fed via a rack from behind the machine.
- Optimal access for changing the fibre rolls
- Active fibre take-off
- End-of-fibre detection
Switching between fibre strands / media
ZSK offers a patented process for automatically switching between two fibre strands. For example, carbon rovings can be placed alternately with glass fibre strands within a component.
The fibre strands can be laid (a) independently of each other, (b) in parallel with HV-TFP or (c) on top of each other.
Carbon fibres can be freely combined with any other fibre, e.g. glass fibre, natural fibre or thermoplastic fibre; Due to the automatic change, wires or fibre optic cables can also be integrated without any problems.
The combination of different materials results in advantages; if, for example, thermoplastic fibres are laid down together with carbon fibre, the resulting TFP preform simply has to be hot-pressed in a mold.
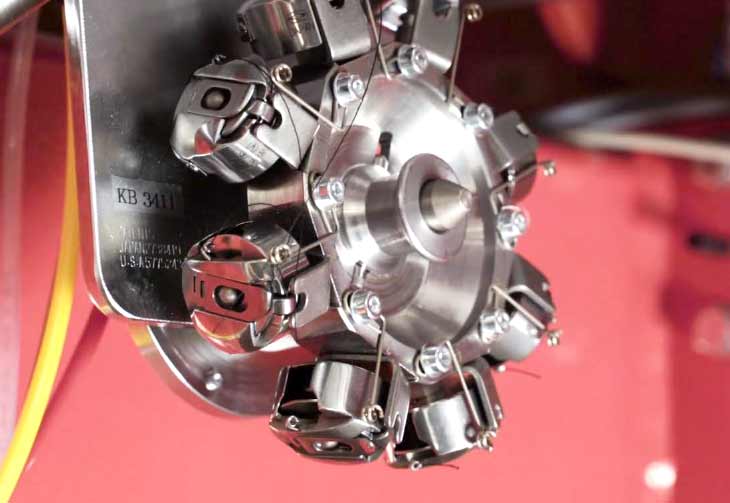
12%
Increase in Up-Time
Automatic bobbin changer
The automatic bobbin changer has a magazine for 8 bobbins. In the T8-2 control unit you can set marker when bobbin changes should take place automatically.
This setup increases the up-time of the machine by approx. 12%.
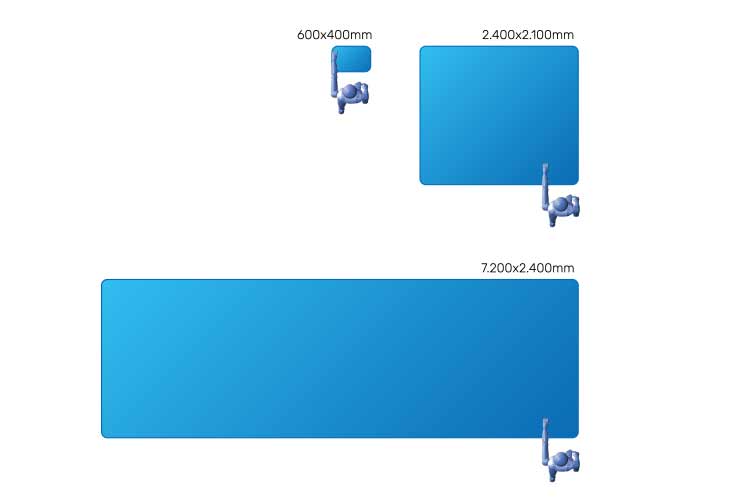
17,3m2
Possible laying field size
Laying fields
ZSK offers machines with the largest laying field. The repertoire of ZSK technical embroidery machines ranges from the smallest TFP machine with a laying field of 600 x 400mm to the largest of 2,400 x 2,100mm. In case of multi-head machines, automatic head switching allows laying fields up to 7.200 x 2.400mm.
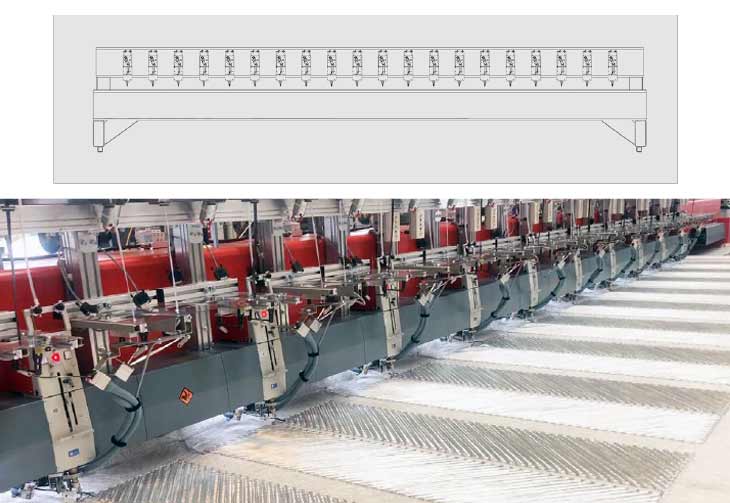
up to 20
components at the same time
Up-Scaling
For mass production of relatively large components, 8-head or 10-head machines have been proven which can place 8 - 10 components at the same time.
For smaller components, machines with up to 20 heads are available.
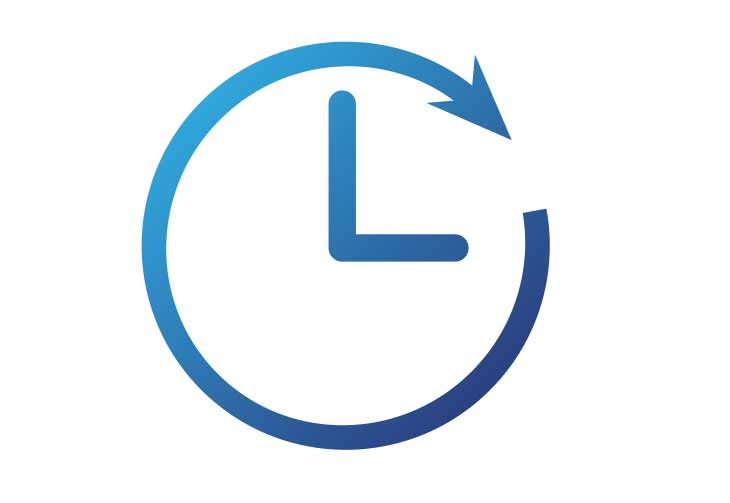
15 Years
running time by 24/7 usage
Carbon protection of the electronics
The electronics of the machine are protected against carbon dust by filters and other preventions.
Reliability
ZSK technical embroidery machines are developed and manufactured in Krefeld. Up to 15 years running time is not uncommon, when using the machines 24/7.
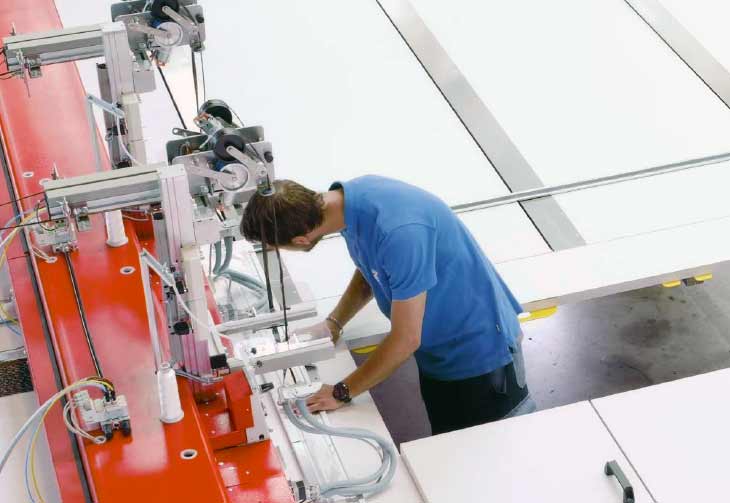
Success
Exchange of knowledge • Training • Prototyping • Production support
ZSK Service and support
Behind the success of ZSK‘s technical embroidery machines is a team with many years of experience. We do not only sell a machine, we are ready to share our experience with our customer. Because only the success of our customers ultimately leads to our success.
ZSK STICKMASCHINEN - Whitepaper
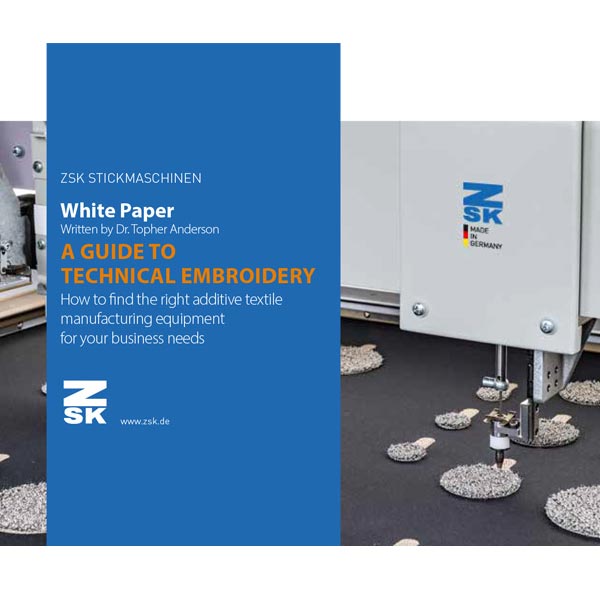
A Guide to Technical Embroidery (PDF) by Dr. Christopher Anderson
How to find the right additive textile manufacturing equipment for your business needs
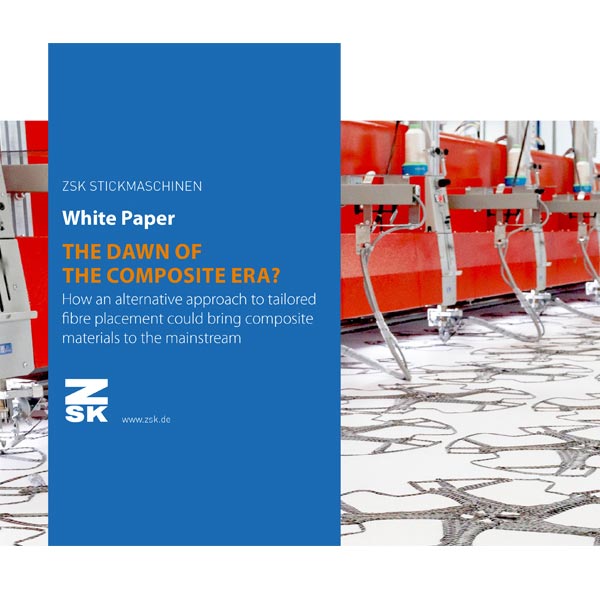
The Dawn of the Composite Era? (PDF)
How an alternative approach to tailored fibre placement could bring composite materials to the mainstream